What Is A Fillet Weld? [All You Need To Know]
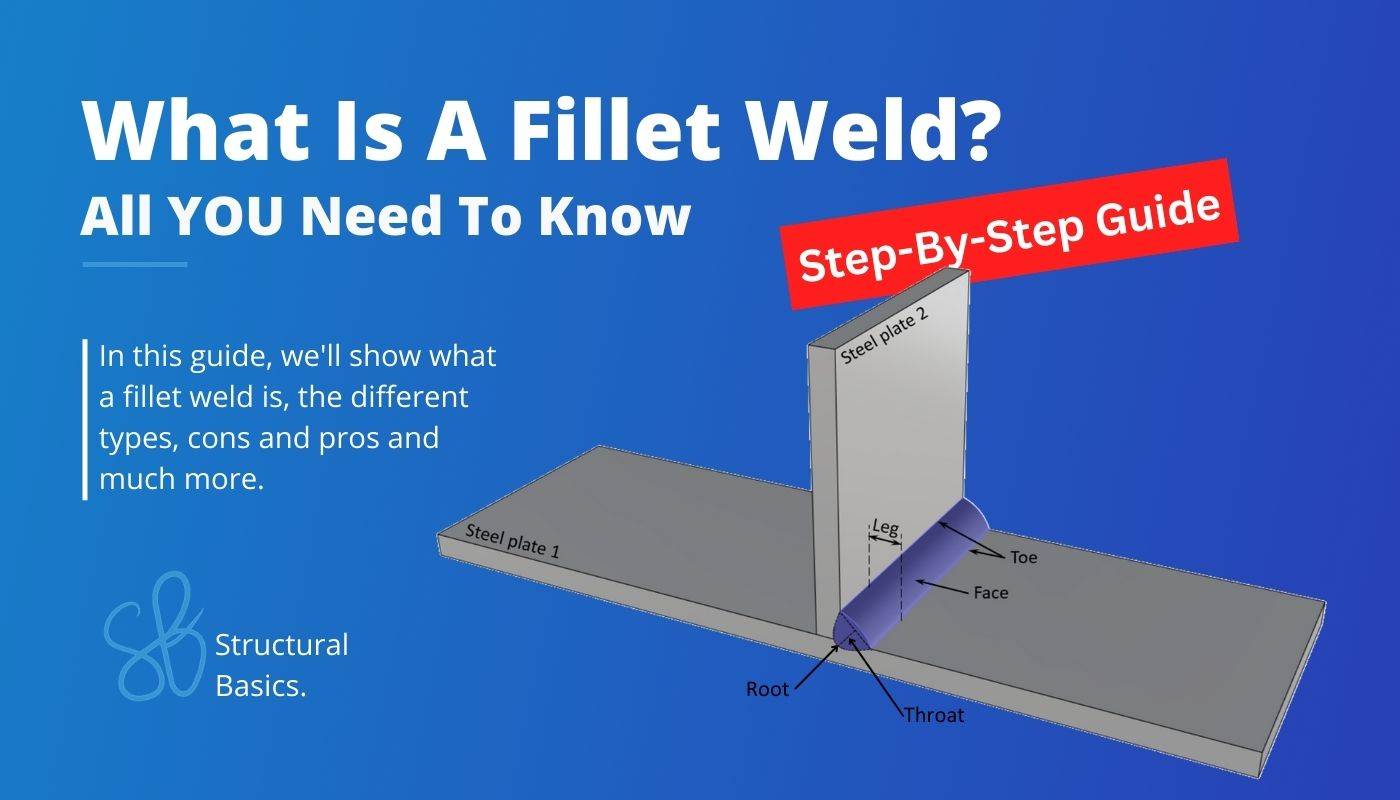
A fillet weld is a type of weld used to join 2 metal pieces by creating a triangular cross-section where they intersect. This creates a strong and seamless bond, commonly used in the construction, manufacturing, and automotive industries for its reliability and structural strength.
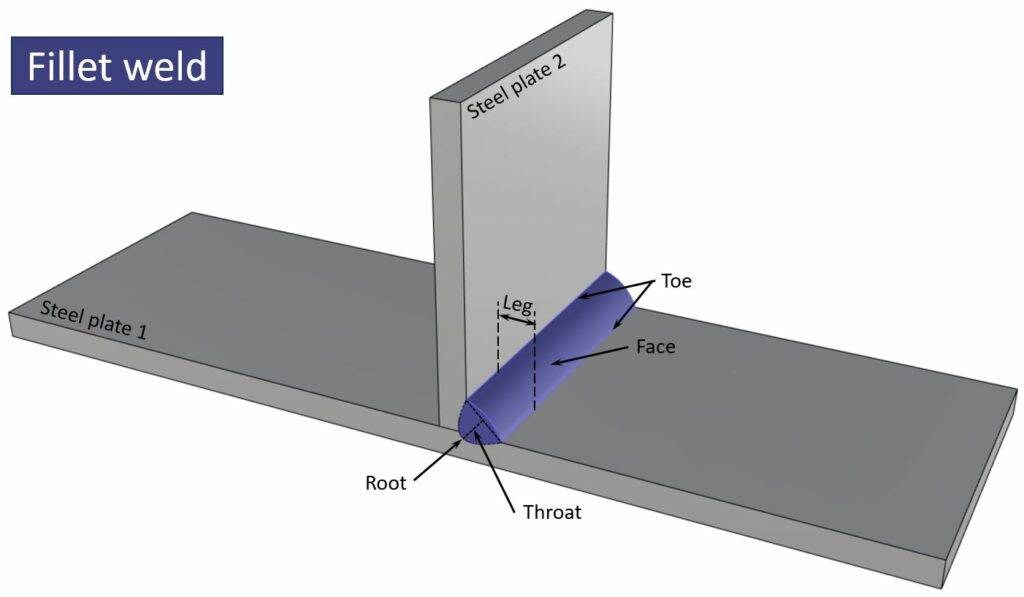
Later in this blog post, we’ll explain more in detail what a fillet weld is, show the different types and applications of butt welds.ππ
We’ll also add real-world examples of steel structures where fillet welds are used. ππ
Alright, let’s get into it. ππ
What Is A Fillet Weld?
A fillet weld is a type of weld used to join two pieces of metal at an angle, typically a right angle. The weld creates a triangular cross-section and fills the gap between the two components.
Fillet welds are commonly used in structural applications, such as buildings, warehouses, bridges, and machinery, to provide strength at joints.
They are known for their simplicity and effectiveness in distributing loads and resisting forces, making them a fundamental welding technique in various industries.
Types Of Butt Welds
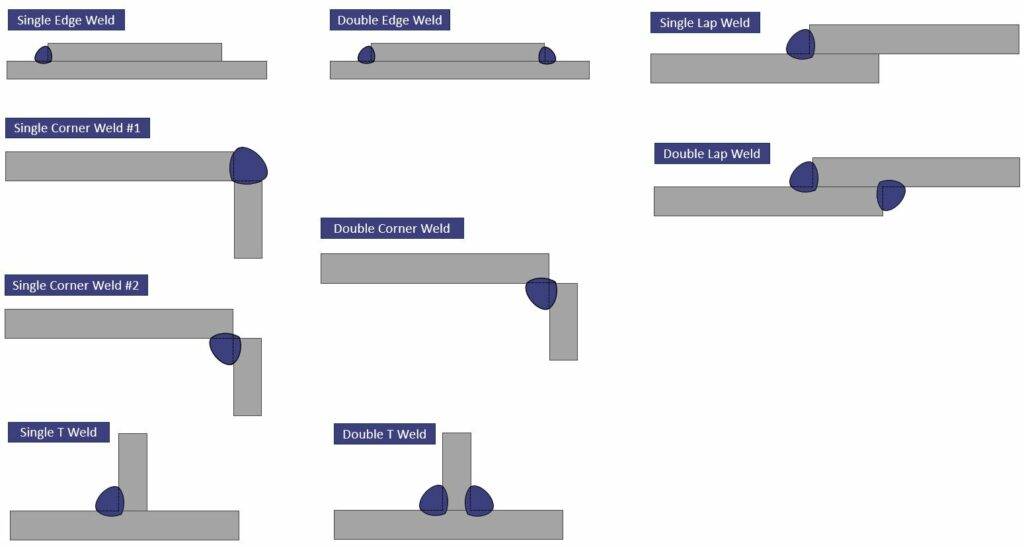
Single T-Weld
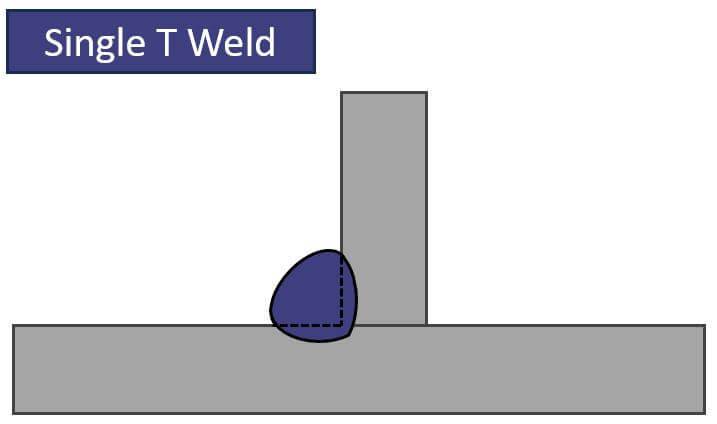
Single Lap Weld
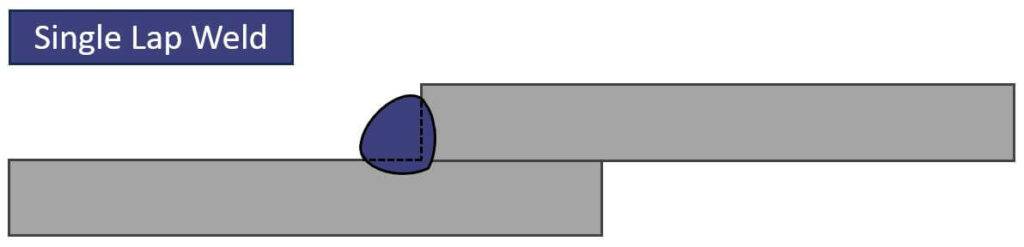
Single Corner Weld #1
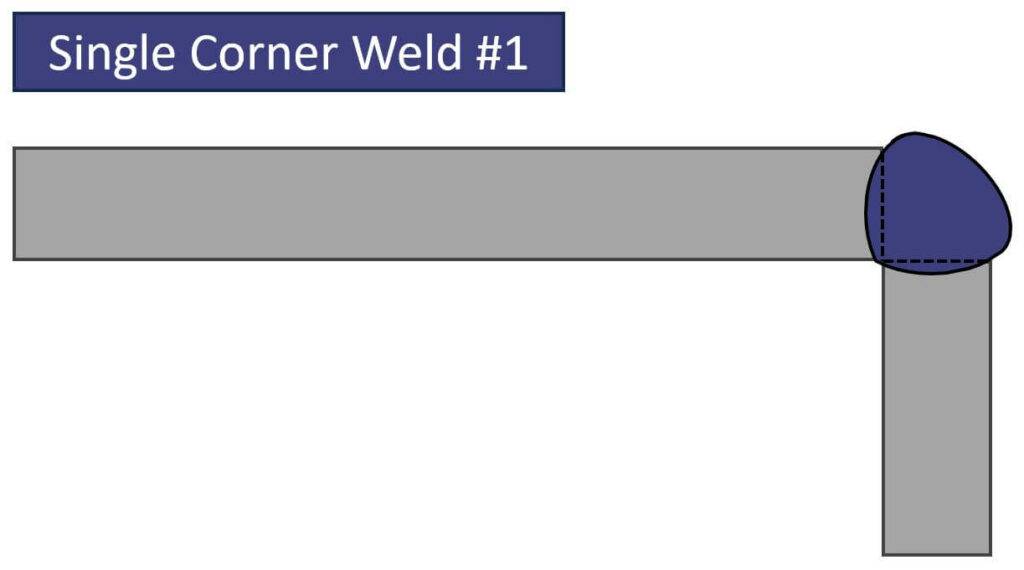
Single Corner Weld #2
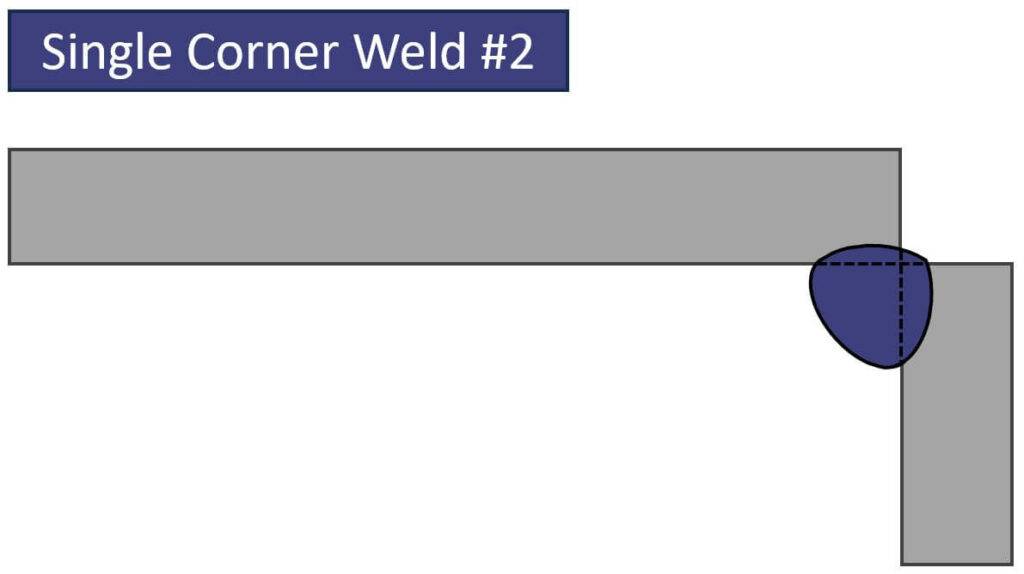
Single Edge Weld
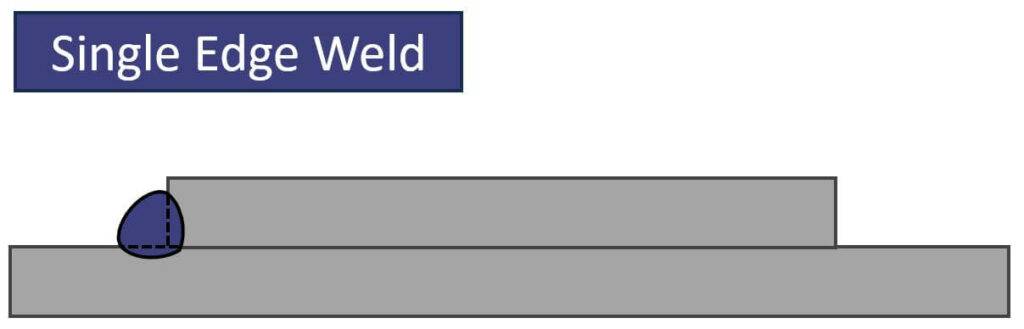
Double T-Weld
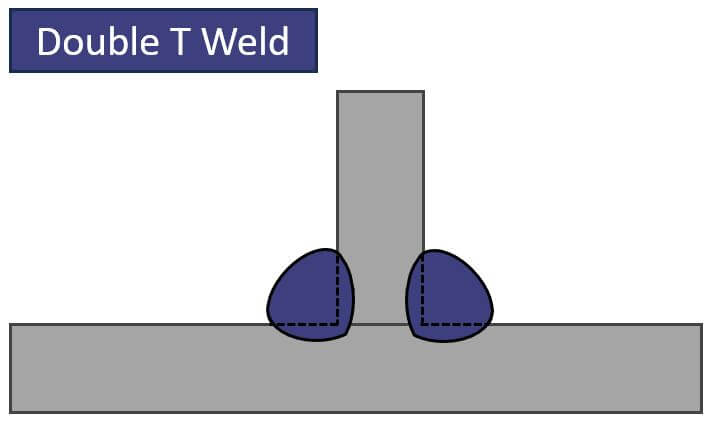
Double Lap Weld
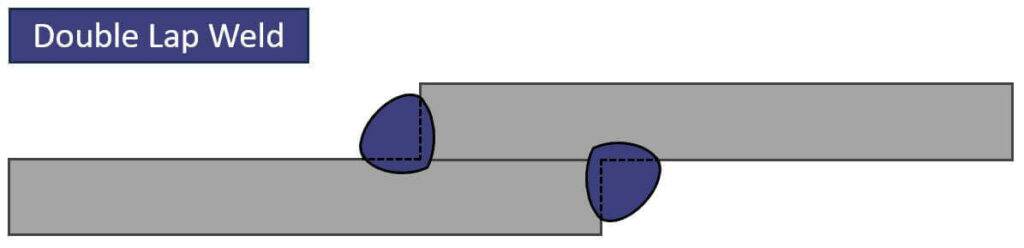
Double Corner Weld
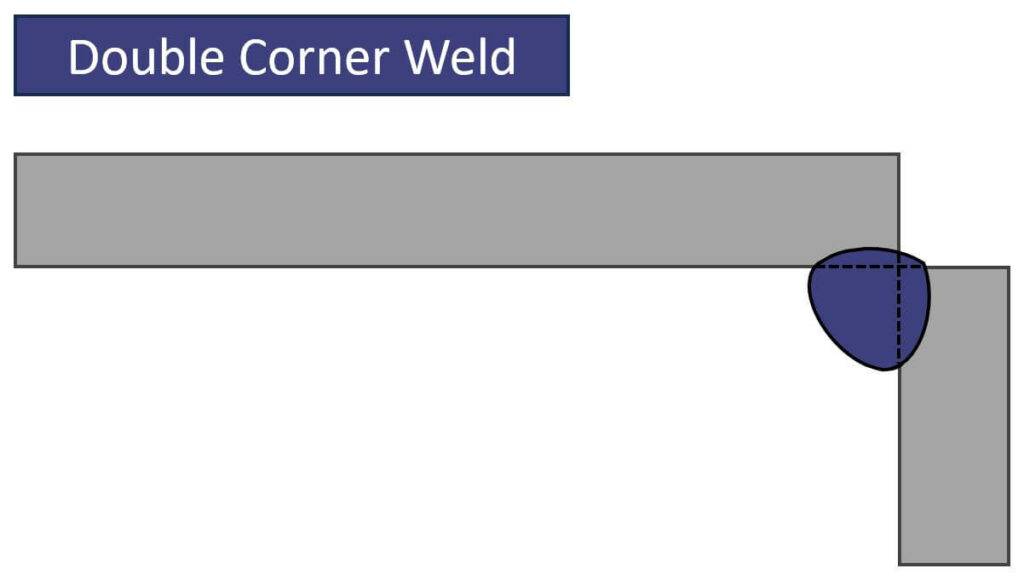
Double Edge Weld
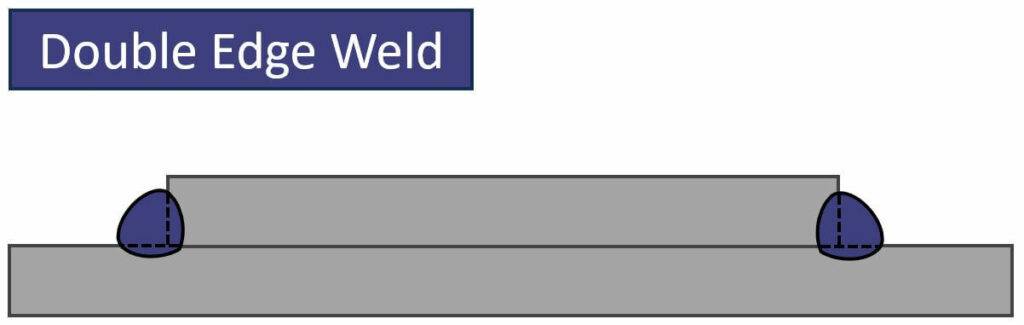
Process Of Fillet Welding
Typically, the following step-by-step process is followed for butt welding. ππ
- Preparation
Ensure that the 2 metal pieces are clean and free of contaminants. In this first step, it’s important that the edges are smooth for a good weld. - Welding setup
The welding machine is set up. Choose appropriate welding parameters, such as current, voltage, and filler material and welding method. - Alignment and clamping
– Place the two steel pieces exactly as they should be welded together.
– Fix the two metals with clamps to prevent movement during welding. - Tack Welding
First, create small tack welds at both ends of the joint to hold the workpieces in place. - Welding
– Start welding by gradually transferring weld material along the length of the joint.
– Multiple passes may be required, with each pass melting and fusing additional filler material into the joint. - Cooling and Solidification
The weld should cool gradually to avoid thermal stresses and distortion.
The act of welding is done now, the following points ensure quality. - Inspection, cleanup, testing and documentation
– After the solidification of the weld, it is inspected for possible defects.
– If needed, the finished weld is cleaned.
– In some cases, destructive and non-destructive tests are executed to verify the strength.
– Document the parameters of the welding and take pictures of the finished weld.
Here’s a good video showing how to weld a butt weld.
Example Of Fillet Welds In Steel Structures
Hinge connection between stiffener plate and SHS100x100x5 profiles
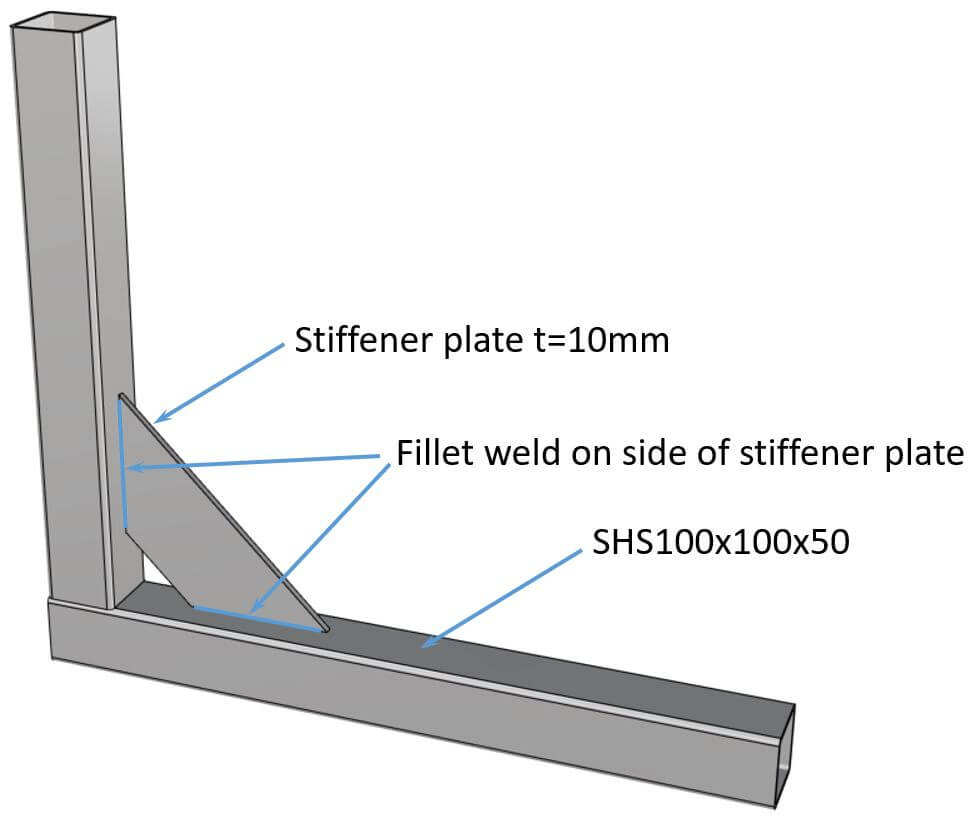
I personally had a similar connection as in the picture above. Fillet welds easy to execute in factories as the welding is “only” added on the sides of the profile and easily accessible.
The verification of this fillet weld should also not be a problem, as only normal forces act in the stiffener. This is because I personally would connect the plate with hinges to the SHS profiles.
Hinge or moment stiff connection between steel column and baseplate
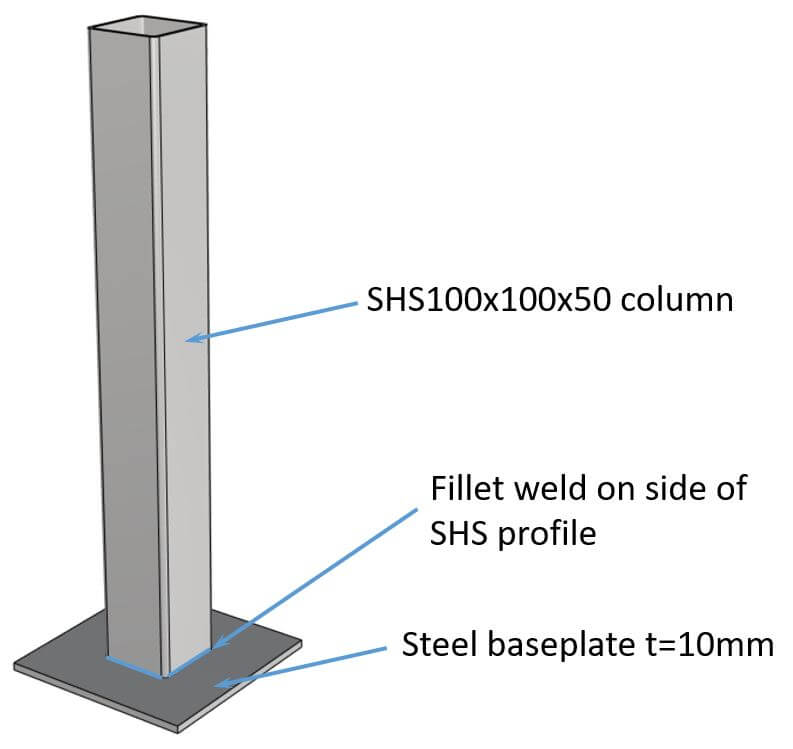
As in the example above, fillet welds are also the preferred choice to connect columns to steel baseplate, as it’s easily accessible from all sides.
Fillet welds, can also take up a moment. So the column could also be fixed.
Pros And Cons Of Fillet Welds
Pros ππ
- Material and cost savings: Fillet welds often require less filler material compared to butt welds, which can lead to cost savings.
- Strength: Compared to some bolt connections, fillet welds have a higher strength
- Versatility: Fillet welds can be used in various joint configurations, such as T-joints, lap joints, and corner joints (as you can see in the images above π)
Cons ππ
- Access limitations: In some cases, accessing the joint to do the weld is impossible.
- Strength: Yes, fillet welds have a good strength resistance, but butt welds provide even higher strength
- Susceptible to defects: If not executed correctly or if the base materials have impurities, fillet welds can be susceptible to defects like cracks.
- Skill required: There are less and less skilled welders, making it challenging to find a contractor to perform the welding job.
- Aesthetics: The shape of fillet welds can be less visually appealing than the flat profile of butt welds.
Application Of Butt Welds
1. Construction industry
- Structural steel structures like warehouses or manufacturing plants: Here fillet welds are used to join beams, columns, plates and other structural members together (like the examples above).
- Pressure vessels: Utilized for the fabrication of pressure vessels, such as tanks, boilers, and reactors.
- Shipbuilding: Used for joining various sections of the hull, bulkheads and other structural components.
- Infrastructure projects: Used in various infrastructure structures, including tunnels, steel bridges, viaducts, and elevated roadways.
- Secondary structures: Fillet welds are utilized for handrails, ladders, and support brackets as they are easily created and have adequate strength.
2. Manufacturing sector
- Machinery manufacturing: Used in the assembly of heavy machinery, manufacturing equipment, and conveyor systems.
- Assembly Line Equipment: Employed for parts of conveyors and robotic workstations.
- Robotics and Automation: Fillet welds are used in the construction of robotic arms and automation equipment.
- Electronics Manufacturing: Assembly of metal enclosures and mounting brackets for electronic components.
3. Automotive and aerospace industry
- Chassis and Frame: Fillet welds are used to join components of a vehicle’s chassis and frame.
- Body Panels: Used to join body panels, such as fender flares, roll cages, and custom body kits.
- Suspension Components: Employed in the assembly of suspension components such as control arms, trailing arms, and axle housings. These welds ensure the proper alignment and strength of the suspension system.
- Aircraft wings: Used in the fabrication of wing structures, including the attachment of wing ribs to wing spars and the assembly of wing fuel tanks.
- Aircraft fuel tanks: The fuel tank, both internal and external, involves fillet welds to create leak-proof seals and structural integrity.
Design Of Fillet Welds
Fillet welds are designed after the steel Eurocode 1993-1-8 4.5.
We are currently working on a step-by-step guide showing how to design fillet welds.
Stay tuned for that!
Conclusion
To summarize, fillet welds are great to join two metal pieces quickly with adequate strength, if you have the space.
They have, however, a lower strength resistance than butt welds, but in turn are easier and in most cases cheaper to construct.
Now, that you got an understanding of fillet welds, you can also learn about butt welds and how to design them.
Usually before you design the welds, you design the steel members such as columns and beams, because you need to know their geometry and internal forces at the location of the connection.
I hope that this article helped you, and you know how to go further from here. In case you still have questions.
Let us know in the comments below. βοΈβοΈ
Fillet Welds FAQ
Fillet welds are commonly used in structural welding for building and bridge structures, automotive manufacturing, aerospace assembly, and in the fabrication of machinery, pressure vessels, and more.
– Easy to create
– Good load-bearing capacity
– Versatility: Fillet welds can be used to join components with different thicknesses and shapes.
The size of a fillet weld is calculated by an engineer. It’s the distance from the root of the weld to the outer surface. The size is typically specified in engineering drawings, making it easy for the welder to know which weld type and size he/she has to use.